RETUBING MACHINE FOR LONG – LINE SYSTEM
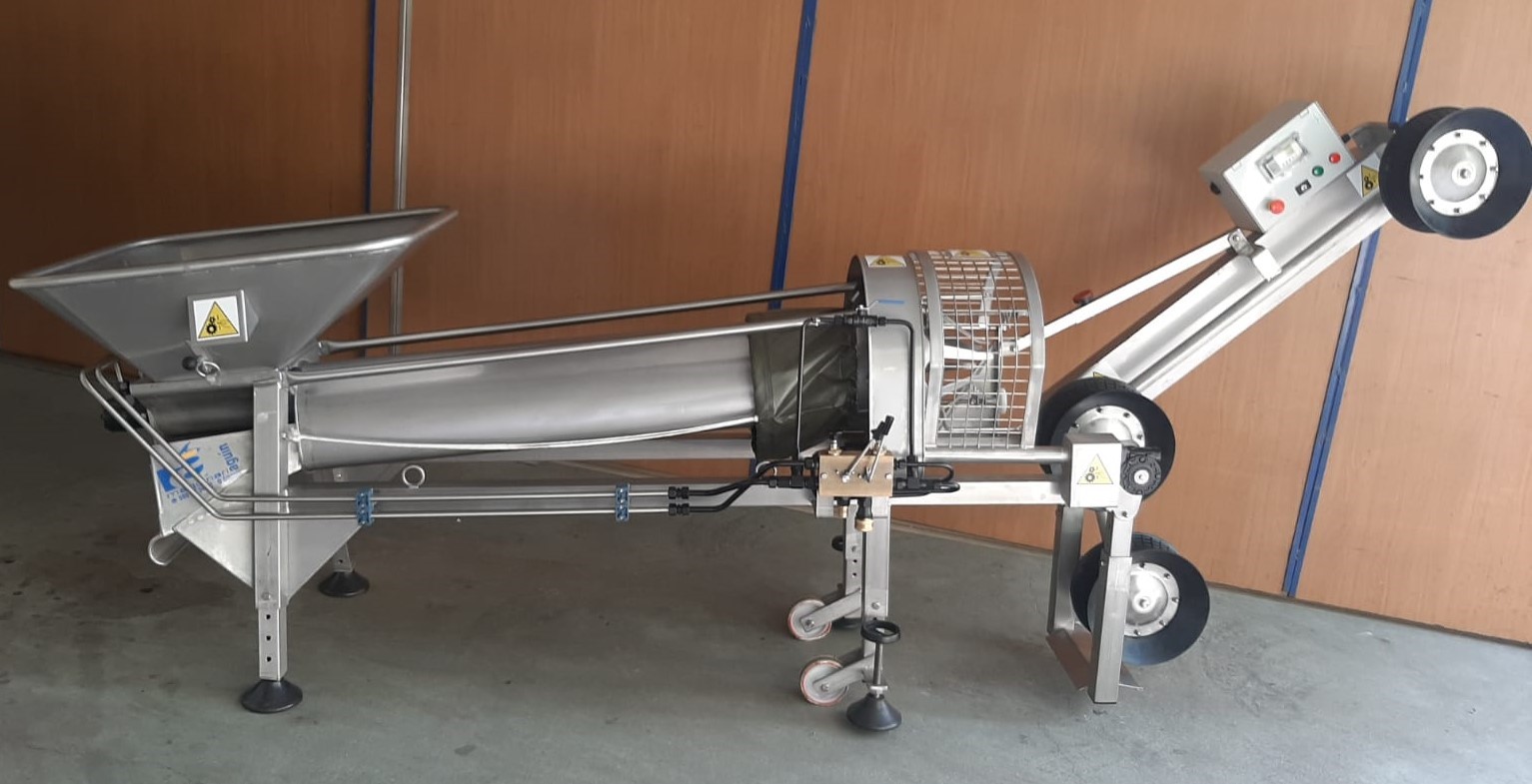
MUSSEL CULTURE: THE CONTINUOS LONG- LINE SYSTEM
The long-line system of mussel culture is probably the method that has evolved the most alongside that of mussel rafts. Both methods have developed many similar techniques with respect to the machinery used.
However, initially the long-line system had many limitations as regards the length of ropes used and the size of the boats. Both these factors made the mechanisation of mussel culture extremely difficult.
Fortunately, these disadvantages have been overcome with the introduction of re-tubing using the continuous long-line system. As a result, we can no longer make negative comparisons between the long-line system and that of mussel rafts in terms of the use of machinery. The first limitations – the lenght of the ropes – is due to the fact the weight each line supports must be carefully controlled. The second limitation regards the size of the vessels, as it must be able to manoeuvre easily between the lines, so it must be considerably small in size. As a direct consequence of this, the lines, so it must be considerably small in size. As a direct consequence of this, the installation of a crane and basket is physically impossible.
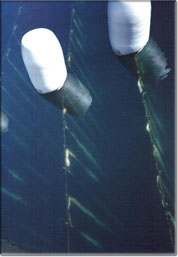
The continuous system overcomes these problems by allowing much smaller boats to be equipped with the machinery to carry out their work quickly and efficiently with a minimum of effort. In this way, it is not difficult considerably to increase cost-effectiveness. Being able to re-tube ropes longer than 500m reduces the amount of time taken to complete the process. This is especially true if compared to the process used until now -that of re-tubing ropes, which are no longer than 10 m, one by one in length.
Now, we will go on to explain the process of mussel culture and the equipment needed for this system, including the different types of vessel used in different areas.
PREPARING THE ROPES
In principle, the lines are already installed at sea and slip knots have been tied onto them from which the ropes will then be hung. The distance between each slip knot is 400 mm, although this can be increased as required. The first step is to prepare the ropes on land. Obviously, we will have to prepare as many ropes as lines already prepared at sea.
We should start by fastening iron rods measuring approximately 10 mm in diameter onto each of the ropes. These rods are the same length as the distance between the slip knots previously tied onto the lines, in this case 400 mm. This is also the distance between the plastic pegs used.
Photograph shows the system of seed collector tapes, to which the iron rods are fixed, currently used in Norway.
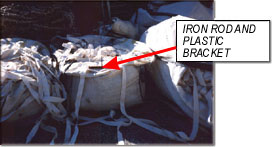
The iron rods are fixed onto the ropes using plastic brackets. Figure 1.
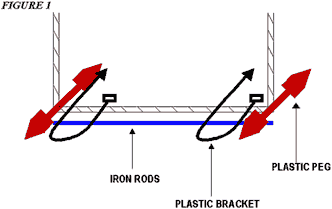
Each rope is 4 m in length. This is the distance between the slip knot on the surface and the iron rod under the sea. The length of an iron rod is the same as the distance between 2 slip knots and as the distance between 2 pegs, i.e. 400 mm. So, we must place 10 pegs, plus one extra for hanging the rope from the line, on each length of rope -a total of 11 pegs per length. Since there are 2 lengths of rope between each 2 iron rods we must use a total of 22 pegs, 2 of which are for hanging the rope from the line. In this way, there will always be the same length of rope on either side of the iron rod. This will ensure that the rods remain horizontal. See figure 2.
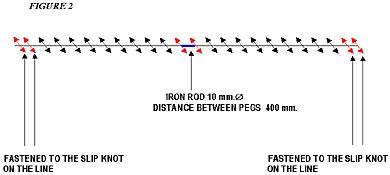
Cables which will support the weight of the ropes are required to fasten them to the line. The cables are tied in a slip knot passed over the peg from which it will be hung. For example, the distance between each iron bar should be twice the height of the rope (4m) plus the length between two slip knots (400 mm). That is to say, 8.4 m.
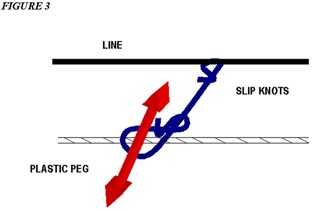
In order to calculate the spacing between each length of rope to be hung, count the number of pegs after the iron bar or use a differently coloured peg to indicate which ones are to be used for hanging the rope. See figure 4
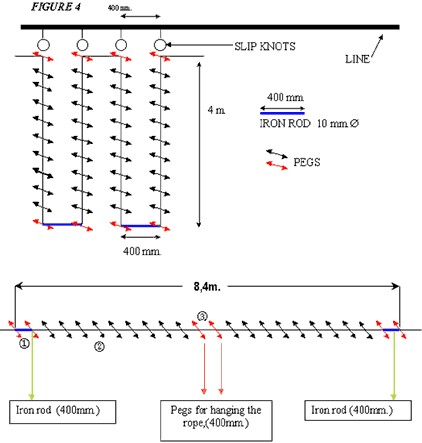
In the previous figure we can see a section of rope prepared on land in detail. It shows a length of rope between two iron rods. We start with the pegs which are fixed on either side of the iron rod (1) and which are of a different colour (usually red). Next, 9 black pegs are attached (2) and then, another red one (3). This peg (3) is the one which will fasten the rope to the line. The next section starts with another red peg for attaching.
COLOURED PEGS TO MARK THE DISTANCE
BETWEEN EACH LENGTH OF ROPE
INSTALLING THE ROPES FROM THE BOAT
When hanging the ropes from the line it is essential to leave a length of line with slip knots but without ropes, equivalent to the approximate length of the vessel. In order to start working, the boat is positioned between the rope laden with mussels and the first slip knot without a rope attached. This is done so that there will not be a surplus of rope laden with mussels within the boat when re-tubing is carried out. As the re-tubing process is being carried out, and we move along the line, this “free” or “empty” section also moves -being progressively displaced towards the other end of the line. So, when theWhen process is finished this “free” section, without ropes hung from it, is at the other end of the line and is ready to be used for re-tubing the next time it is carried out but, this time, in the opposite direction.Obviously, when the start of the line is at the bow, the first length of rope to be re-tubed will appear over the stern. So, the first newly re-tubed rope must be hung from the first slip knot at the bow.
Thus, when re-tubing starts, there will be a length of line without any ropes attached from which the first rope is to be hung. Consequently, the length of rope that we pull on board for re-tubing does not pile up inside the boat because the “free” section of the line is on board and the surplus is unloaded over the bow, already re-tubed, with a difference of two to three lengths of rope.
If this is not done in this way, we would have a length of line as long as the boat itself on board with all its mussel laden ropes attached while we are re-tubing.
For example, if the vessel is 5 m in length and two 4 m lengths of rope are attached every metre, there would be 40 m of rope loaded with mussels on board. (5 x 2 x 4 = 40) This would make manoeuvring extremely difficult and would have negative repercussions on the efficiency of the re-tubing process. (See figure 5).
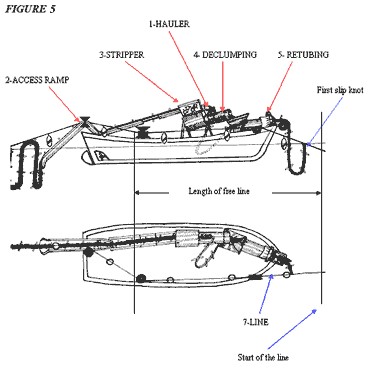
RE-TUBING
Vessels must be specially adapted for re-tubing. The first step is to install an access ramp. Straight after the ramp, there is a device to detach the mussels which, although self-contained, works in conjunction with the hauler. It is powered by a hydraulic pump, fitted to the boat’s engine.
A roller to carry the line overboard is installed at the bow. The access ramp has an incorporated vertical roller which controls the line at the stern.
Figure 5 shows the bow roller, which is displaced to starboard to provide more space for manoeuvrability, and the stern roller, which is fitted to the ramp. The ropes are pulled out of the water and up the ramp by the hydraulic hauler (1).
A device to pull the mussels off the rope has been inserted between the hauler and the ramp. It drops the mussels into the de-clumping machine (4) to be de-clumped and graded before passing into the re-tubing machine (5) from which the new, re-tubed rope will emerge to be fastened once more onto the line (7) as it passes over the bow.
Once the re-tubing process is complete, the ropes, which have now been hung from the line, are covered by perfectly graded mussels, free of parasites, which slowed down growth rates. This promotes more uniform growth and an increase in the quality of the product.
Although we have described the continuous re-tubing process in general terms, it is also possible, depending on circumstances, to carry out the processes of collection, de-clumping and re-tubing independently of one another.
ELEMENTS USED IN THE PROCESS
The equipment used in the continuous re-tubing process consists of four fundamental devices, two of which, the de-clumping machine and the re-tubing machine, are also used in other culture systems such as non-continuous long-line and mussel rafts.
- THE DE-CLUMPING MACHINE, this machine de-clumps and grades mussel in a single operation with a yield of up to 4,000 kg/hour. Both the speed of de-clumping and the size of mussel to be graded can be regulated. It is driven by a hydraulic motor OMP 200. It weighs approximately 50 kg and is manufactured in stainless steel.
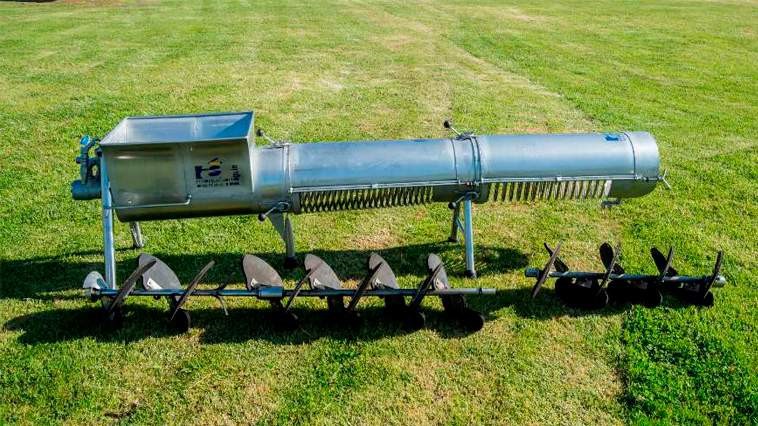
-
THE RE-TUBING MACHINE, has an output of 1m/second of re-tubed rope- the diameter of which can be adjusted as required. It has a speed control knob, a stop-start device and its height can be adjusted. It is powered by two hydraulic motors, OMP 50 and OMP 32, and is manufactured in stainless steel.
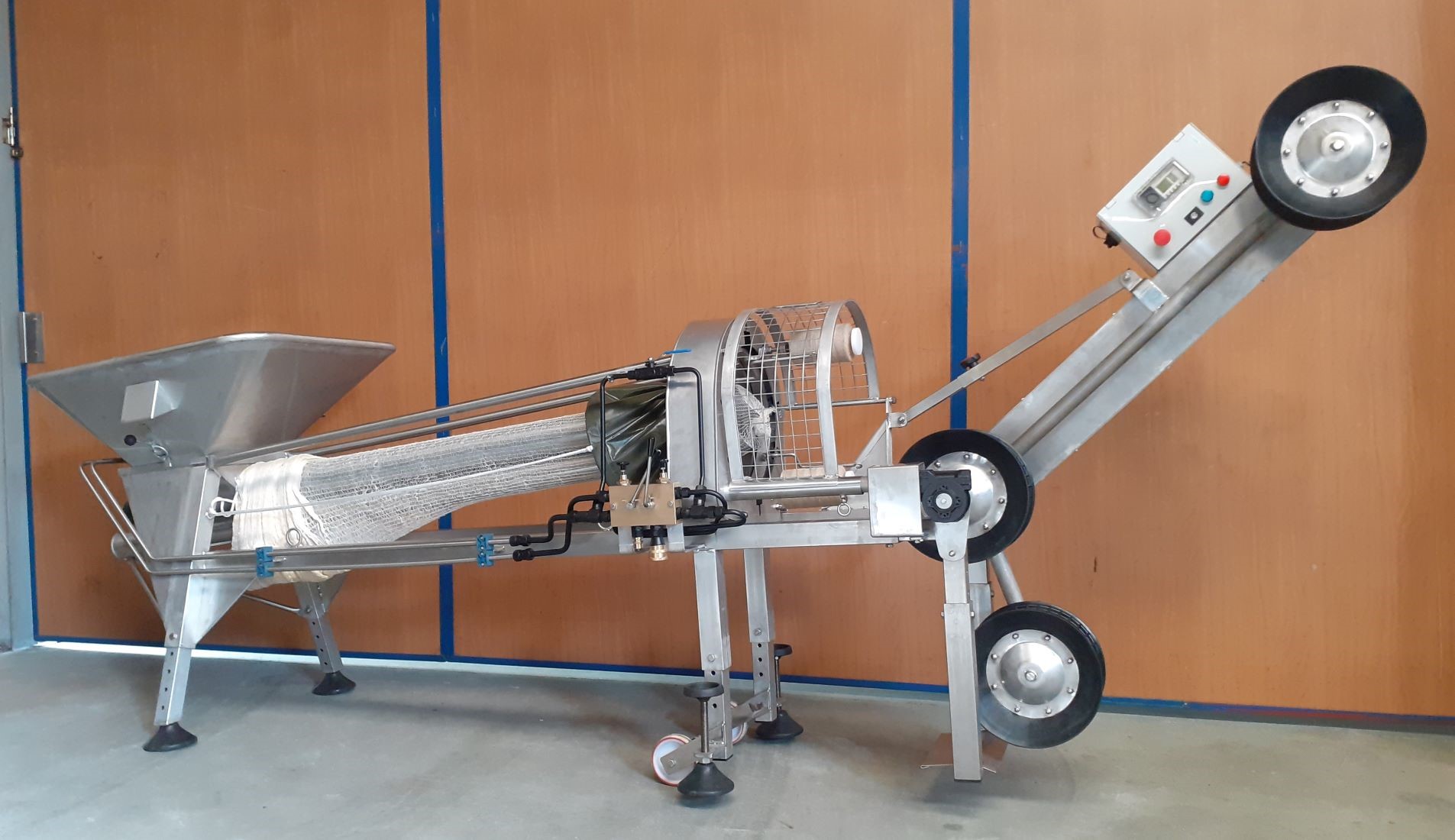
CHOOSING A SITE
Although the site conceded is normally controlled by the government, it is essential that it offers optimum conditions for the development of the mollusc and, in addition, that it is not over-exposed to surf, swell or storms that could seriously affect the day-to-day work of mussel culture.
Another factor to be taken into account is the depth of the water. If it is too shallow, it would limit the length of the ropes. Also, in warmer regions, like the Mediterranean, the temperature of the water can be so high as to threaten the survival of the mussel.
In areas which are rich in plankton a faster rate of growth is achieved and, for this reason, water analysis is another important point to bear in mind when choosing the best site for mussel culture.
IMPLANTING A MUSSEL CULTURE FOR THE FIRST TIME
When implanting a mussel culture for the very first time in an area where it has never existed, the use of ropes for seed collection is not recommended. This is because if adult mussels are absent in the area, no spawning can have taken place and, as a result, the amount of seed collected would be practically zero.
In these cases, it would be advisable to use seed collected from another area or collected from rocks.
In each successive harvest the amount of seed collected will increase until the required quantity is reached, as long as the area provides the necessary conditions.
The fixing of seed collected from rocks to the ropes is done by hand, without paying too much attention to the overall form of the re-tubing, as small seed can move around the rope very easily and will cover it in a very short time. The same is true of small seed (1 cm) from seed collectors.
However, when the seed to be re-tubed is bigger than 2 cm. it is advisable to cover the rope uniformly to a diameter of not more than 10 cm, approximately. If the seed is even larger (3-4 cm.) the diameter of a re-tubed rope can be between 10 and 13 cm. In this case the re-tubing machine can be used. The re-tubing process can be carried out in a number of ways depending on the amount of seed available and the place where the ropes are to be located.
It is not advisable to keep the seed out of the water for very long, especially in high temperatures. We have to take into account that it will be handled during de-clumping and grading, and, that these processes will lead to the loss of part of the water inside the seed. This can have a negative effect on the seed, slowing its growth until it recovers from the damage incurred during de-clumping and re-tubing. Generally speaking, however, handling will not lead to the mussel dying.
This is one of the reasons which have led us to improve the way the de-clumping machine works on the mussel. We have managed to make the process more gentle to avoid some of the loss of water and, so, provide more favourable conditions for the mollusc.
Whenever possible, we would recommend that re-tubing be carried out immediately after extracting the seed from the water. This is one of the factors that makes the continuous long-line system so suitable as it allows us to keep the seed out of the water for very brief periods.
Another of the advantages of this system is that it does not require a great amount of space within the vessel to carry out these tasks. This is very important if small vessels are to be used.
Depending on the amount of seed collected there will, obviously, be an important quantity of surplus, which will have to be placed on new ropes between lines. It should be taken into account that re-tubing is usually carried out with a third of the seed from the seed collectors. For this reason, it is useful to have “empty” lines from which to hang the new ropes obtained with the surplus seed.
GRADING THE SEED
During the re-tubing process the seed must be de-clumped and graded to obtain a uniform size of seed while simultaneously eliminating any parasites. Sometimes there is a great amount of very small seed mixed up with the parasites, which have passed through the de-clumping machine’s grating. The best way to separate them is to put this mixture through a grading table, which has previously been adjusted to the required size. As the seed is loose, it is easy to separate it from the parasites by simply pushing it across the grating on the grading table.
Once we have this smaller seed, which has already been graded by the de-clumping machine, we can re-tube it onto new ropes taking care not to mix it with the other, larger seed and then place these new ropes in a different area as the smaller seed will need longer to develop.
RETUBING
When carrying out the re-tubing process it is important to remember that the seed should be free of the net as soon as possible in accordance with the conditions provided by each site. In fairly calm areas, if the seed has a strong enough beard (byssus thread), binding the re-tubed rope with cord will be sufficient. However, in areas where the mussel is easily detached by the swell, or if it does not have a strong beard, a net should be used. Depending on the ease with which the mussel is detached, the net can be cotton, acetate, nylon or a nylon-acetate mix.
THE ROPE.
After many years of experience we have reached the conclusion that the most suitable rope for re-tubing is one made from net and plaited with plastic pegs. Due to the large number of knots and loose ends it has, this type of rope constitutes an excellent base for the mussel to fasten onto. The characteristics of this type of rope as regards strength, durability and reliability prove it to be the most suitable, both for the mussel raft system and for the long-line system.
The rope used is made of two lengths of plaited net with a finished diameter of 16 mm.
HARVESTING
Harvesting the mussels for sale is done in the same way as previously explained for re-tubing.
The ropes laden with mussels are pulled up the access ramp and the mussels are detached from the rope by device 3. This rope, which has been removed from the line by loosening the slip knot, will be fastened to the line again and will return to the sea as if it were laden with mussels. Now it is ready for use either as a seed collector or for introducing seed into the culture again.
It is best to prepare mussels for sale on land or on a rig at sea otherwise there is not enough room to store what has been harvested on board and the vessel would be overloaded with the machinery required to prepare it. So, as mentioned above, de-clumping, washing and packing should be carried out on land or on a rig using the de-clumping machine and grading table.
By keeping the vessel nearby, we can use it for connecting the hoses with which to work the machinery. If the vessel is big enough to carry out these tasks on board, there is no doubt that the whole process would not only be quicker, but also, more convenient.
ADVANTAGES OF THIS SYSTEM.
Among the various advantages of the continuous long-line system using the above-mentioned machinery the following are paramount:
-
The simplification of the re-tubing process as it is carried out in a single operation and the possibility of being able to do this in situ. (See photographs 5, 6, 7 and 8 of the older non-continuous system).
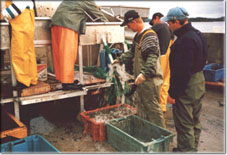
-
The speed and ease with which ropes laden with mussels can be raised.
-
The fact that mussels can be removed from the ropes with a minimum of effort as the hydraulic hauler pulls the rope out of the water.
-
The machinery needed is of reduced size and weight and can, therefore, be used on smaller vessels. (See photographs 9 and 10 for other equipment used).
- The low cost of the equipment.
-
The fact that the equipment is low-tech and simple to use from the moment it is introduced. In addition to this, it is virtually breakdown-free so there is no dependency on a supplier for after-sale service.
-
The use of ropes with pegs prevents the mussels becoming detached. When smooth ropes are used up to 50% of the product can be lost. (See photograph 11) The use of pegged ropes also means the producer does not have to resort to bagging the ropes while the mussel is growing -a process which can slow down its development. (See photograph 12).
-
The fact that pegged ropes can be used over and over again. This cannot be done with ropes re-tubed inside permanent netting. This also prevents the formation of non-biodegradable residues which benefits the ecosystem. (See photograph 13)